KRL045DLS2114NNN3C2NGA6NKNBNNNNNN danfoss pump
KRL045DLS2114NNN3C2NGA6NKNBNNNNNN danfoss pump

- Product Details
- Applicable Scene
Sauer Danfoss hydraulic pumps are renowned for their reliability and efficiency in a variety of applications, from agricultural machinery to industrial equipment. To ensure the optimal performance of these pumps, regular maintenance and careful operation are essential. Here are some key practices to help keep your Sauer Danfoss hydraulic pumps running smoothly.
KR-L-045D-LS-21-14-NN-N-3-C2NG-A6N-KNB-NNN-NNN
KRL045DLS2114NNN3C2NGA6NKNBNNNNNN
Firstly, regular inspection is crucial. Check the pump for any signs of leaks, unusual noises, or vibrations. These could indicate underlying issues that need immediate attention. Additionally, monitor the hydraulic fluid level and quality regularly. Contaminated or insufficient hydraulic fluid can lead to poor performance and excessive wear on the pump components.
7004673S
Secondly, ensure that the hydraulic system is properly filtered. A good filtration system helps to remove contaminants from the hydraulic fluid, extending the life of both the fluid and the pump. Change filters according to the manufacturer’s recommendations or sooner if you notice a decrease in performance.
Furthermore, maintaining the correct hydraulic fluid temperature is important. Operating the pump in extreme temperatures can cause thermal degradation of the fluid, leading to increased wear and tear on the pump. It’s advisable to keep the fluid within the recommended temperature range, which is typically indicated in the pump’s specifications.
Another critical aspect of pump maintenance is lubrication. Make sure that all moving parts are adequately lubricated based on the manufacturer’s guidelines. Proper lubrication reduces friction, which in turn minimizes mechanical wear and prolongs the life of the pump.
Regularly check the alignment of the pump with the motor and other connected components. Misalignment can cause excessive stress on the pump, leading to premature failure. Utilize alignment tools to ensure that all components are correctly aligned and functioning harmoniously.
In addition to these practices, it is essential to keep detailed records of maintenance activities, including inspections, fluid changes, and any unusual observations. This documentation can help identify patterns or recurring issues, leading to proactive solutions and informed future actions.
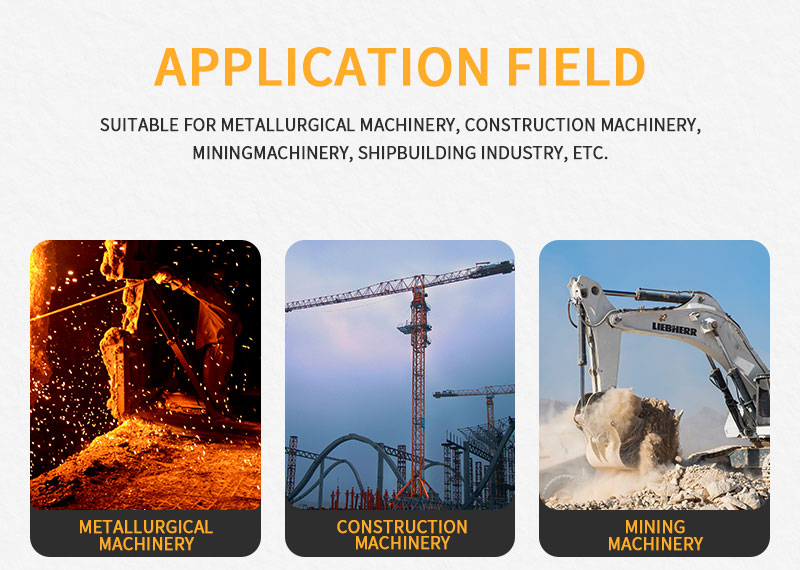
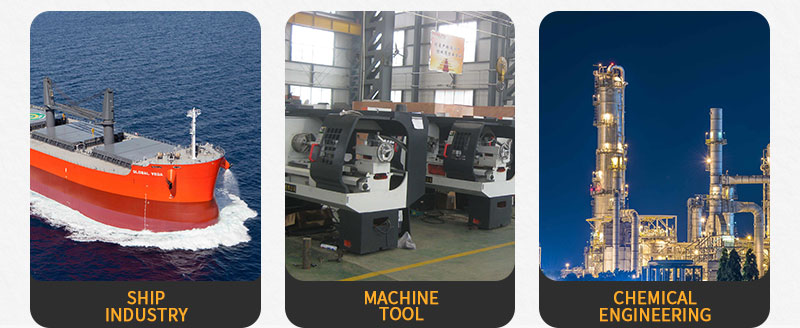