ERR130BRP2620NNN3S4CPA1NAAANNNNNN danfoss pump
ERR130BRP2620NNN3S4CPA1NAAANNNNNN danfoss pump

- Product Details
- Applicable Scene
Hydraulic pumps are essential components in many industrial and construction applications, powering equipment such as excavators, forklifts, and manufacturing machinery. However, the powerful forces they unleash can also pose significant risks if safety measures are not diligently observed. To ensure a safe working environment and prevent accidents, it is critical to adopt best practices related to hydraulic pump safety.
ER-R-130B-RP-26-20-NN-N-3-S4CP-A1N-AAA-NNN-NNN
ERR130BRP2620NNN3S4CPA1NAAANNNNNN
One of the most effective ways to prevent accidents is through regular maintenance. Hydraulic systems should be inspected periodically for leaks, wear, and damage. Any signs of fluid leaks can lead to hazardous conditions, including slipping hazards or reduced system performance. Maintenance checks should include examining hoses, seals, and connections to ensure everything is in proper working order. Moreover, maintenance should always be performed by qualified personnel familiar with hydraulic systems.
80005958
Proper training is another cornerstone of hydraulic pump safety. All operators and maintenance personnel should receive comprehensive training on the specific equipment they will be working with. This training should include understanding the function of hydraulic pumps, potential hazards, proper operating procedures, and emergency response actions. Operators should also be well-versed in reading equipment manuals and safety data sheets for the fluids being used in the system.
Safety gear plays an instrumental role in protecting personnel from potential injuries. It is essential for workers interacting with hydraulic pumps to wear appropriate personal protective equipment (PPE) such as gloves, safety glasses, and steel-toed boots. In addition, face shields should be considered when working in close proximity to hydraulic systems under pressure, as high-pressure fluid can cause serious injuries.
Another best practice is to implement lockout/tagout (LOTO) procedures during maintenance and repair work. This technique ensures that hydraulic pumps are completely shut down and cannot be inadvertently restarted while maintenance is in progress. Lockout/tagout devices should be applied to all energy sources associated with the system, and clear communication among team members is crucial to ensure that everyone understands when it is safe to work on the hydraulic system.
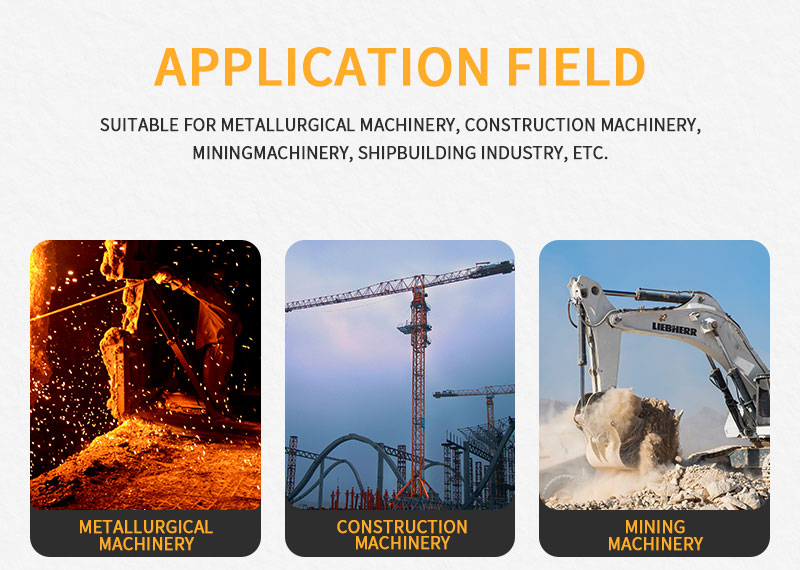
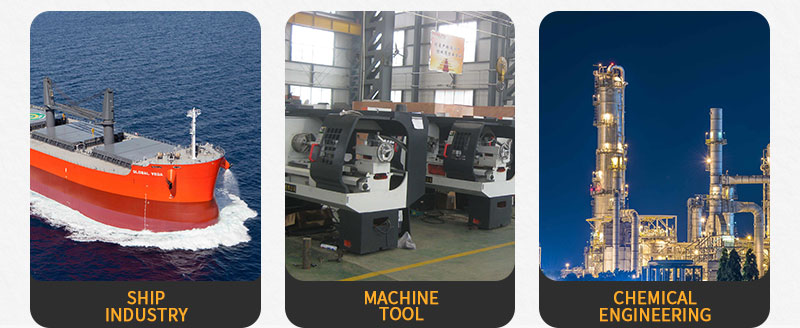