90L055KA1CD80R3S1D03GBA232324 piston pump
90L055KA1CD80R3S1D03GBA232324 piston pump

- Product Details
- Applicable Scene
The textile industry has experienced remarkable advancements over the years, particularly with the introduction of high-speed knitting machines. These machines demand precise and efficient operations, and hydraulic systems play a crucial role in their functionality. Designing hydraulic oil pumps that can meet the specific requirements of high-speed knitting machines is essential for enhancing productivity and ensuring smooth operation.
90-L-055-KA-1-CD-80-R-3-S1-D-03-GBA-23-23-24
90L055KA1CD80R3S1D03GBA232324
Hydraulic oil pumps are vital components in these machines, responsible for providing the necessary fluid power that enables movement and operation. The design of these pumps must take into account several factors, including flow rate, pressure, efficiency, and compatibility with hydraulic fluids. In this article, we will explore some key considerations for designing hydraulic oil pumps tailored for high-speed knitting machines.
80006182
One of the primary considerations in hydraulic pump design is flow rate. High-speed knitting machines often operate at accelerated speeds, requiring hydraulic systems that can deliver fluid rapidly and consistently. Engineers need to calculate the required flow rates based on the machine’s operational speeds and the number of functions that the hydraulic system must perform. This ensures that the pump can sustain the necessary pressure and maintain machine efficiency during operation.
Pressure capability is another critical aspect. The hydraulic system’s pressure must be sufficient to support the various movements and operations of the knitting machine, such as yarn tensioning, fabric feeding, and needle actuation. Designers must ensure that the hydraulic pumps can withstand the operational pressures found in these systems without faltering. This often involves selecting robust materials and innovative designs that can handle the stress and fatigue associated with high-speed operations.
Efficiency is also a vital consideration in pump design. Designers should aim to minimize energy loss within the hydraulic system to reduce operational costs and environmental impact. High-efficiency hydraulic pumps can convert a greater proportion of the input energy into useful work, leading to reduced energy consumption. Implementing advanced technologies such as variable displacement pumps or gear pumps with optimized profiles can enhance efficiency and provide better performance in high-speed applications.
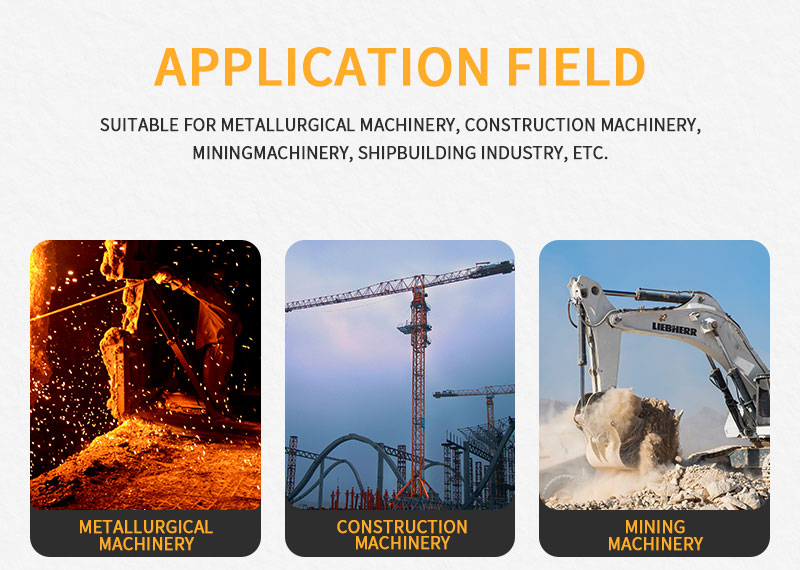
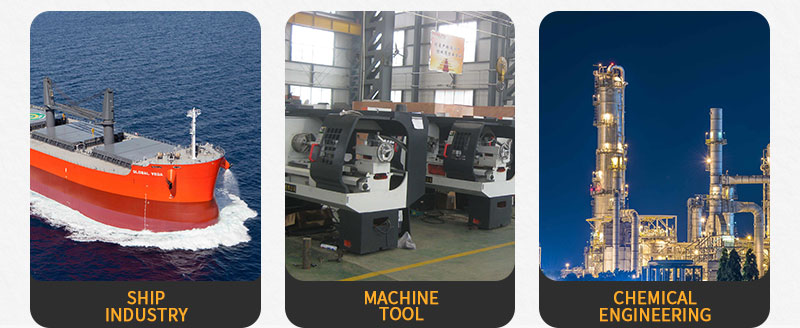