90L055KA1NN80P3C6C09GBA454520 hydraulic pump
90L055KA1NN80P3C6C09GBA454520 hydraulic pump

- Product Details
- Applicable Scene
Hydraulic press systems play a critical role in various industrial applications, ranging from metal forming to food processing. At the heart of these systems lies the hydraulic oil pump, which is essential for converting mechanical energy into hydraulic energy. The design of hydraulic oil pumps for such systems is a significant engineering challenge, requiring careful consideration of efficiency, reliability, and adaptability to automation technologies.
90-L-055-KA-1-NN-80-P-3-C6-C-09-GBA-45-45-20
90L055KA1NN80P3C6C09GBA454520
One of the primary factors in designing hydraulic oil pumps is the selection of the pump type. Common types include gear, vane, and piston pumps, each with distinct advantages and disadvantages. Gear pumps, for example, are robust and provide a steady fluid flow, making them ideal for applications requiring consistent pressure. On the other hand, piston pumps offer higher efficiency and pressure capability, suited for high-demand operations in automated environments. The choice of pump should align with the operational requirements and the specific characteristics of the hydraulic press system.
80006673
Efficiency is another critical aspect of hydraulic pump design. A well-designed hydraulic oil pump must minimize energy losses during operation, which is essential for reducing operational costs and enhancing system performance. Factors that impact efficiency include the pump’s volumetric efficiency, mechanical design, and the type of hydraulic fluid used. Engineers often employ advanced modeling techniques and simulations to optimize the pump design, ensuring it meets the necessary performance criteria while using the least amount of power.
Reliability is paramount in automation, where downtime can lead to significant production losses. Hydraulic oil pumps must be designed to withstand the rigors of continuous operation, including factors such as temperature fluctuations, pressure variations, and contamination. Using high-quality materials and implementing robust sealing technologies can mitigate the risks of wear and tear, ensuring longevity and reducing maintenance costs. Additionally, incorporating monitoring systems can provide real-time data on pump performance, enabling predictive maintenance and minimizing unexpected failures.
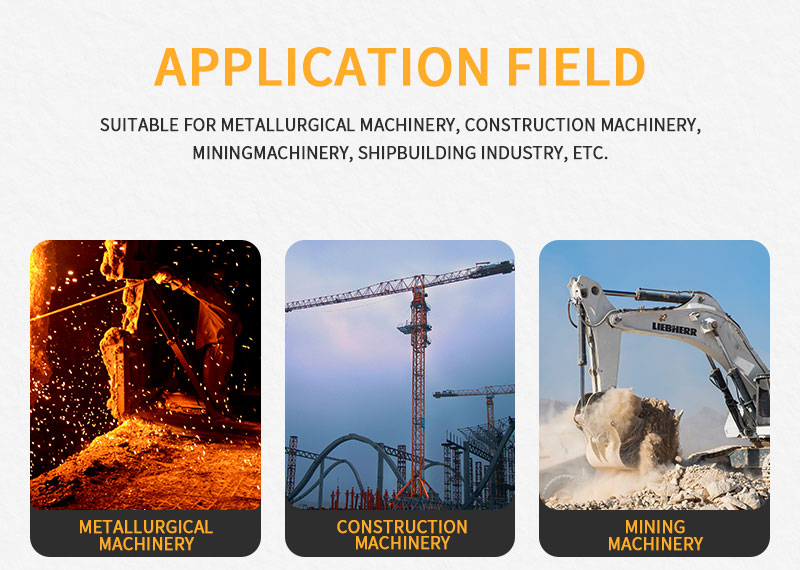
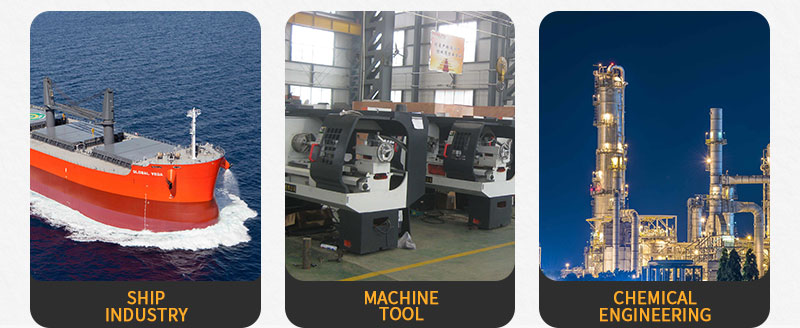