90L055KA5BC60L3S1C04GBA353524 high pressure pump
90L055KA5BC60L3S1C04GBA353524 high pressure pump

- Product Details
- Applicable Scene
The offshore oil and gas industry heavily relies on advanced technologies to ensure the efficient extraction of resources from beneath the sea. One of the critical components in offshore operations is the hydraulic oil pump, which plays a pivotal role in positioning and movement control of oil rigs. This article explores the essential design considerations, challenges, and innovations associated with hydraulic oil pumps used in offshore oil rig applications.
90-L-055-KA-5-BC-60-L-3-S1-C-04-GBA-35-35-24
90L055KA5BC60L3S1C04GBA353524
Hydraulic systems are fundamentally responsible for converting hydraulic energy into mechanical energy, facilitating various movements and functions on an oil rig, such as hoisting equipment, anchoring, and dynamic positioning. This conversion is achieved through hydraulic oil pumps, which must be designed to handle the specific demands of the offshore environment.
702896
One of the primary design considerations for hydraulic oil pumps is their ability to operate effectively under extreme conditions. Offshore oil rigs are subjected to harsh weather, high pressures, and corrosive seawater. Therefore, the materials used in the construction of hydraulic oil pumps must resist corrosion and wear. The use of high-grade stainless steel and specialized coatings can enhance the durability of pumps, ensuring they maintain performance over extended periods.
Another critical aspect is the pump’s efficiency. As operational costs are a significant concern in the offshore industry, designing hydraulic oil pumps with high energy efficiency can lead to reduced fuel consumption and lower operational costs. Innovative pump design features such as variable displacement mechanisms can optimize performance by adjusting to the pressure requirements of the system. This adaptability ensures that the pump operates efficiently, regardless of fluctuating environmental demands.
Furthermore, the integration of advanced control systems is crucial in modern hydraulic pump design. Automation and digital monitoring systems enhance the precision and responsiveness of positioning and movement control. By incorporating sensors and feedback loops, operators can achieve real-time monitoring of system performance, enabling them to make informed adjustments and improvements. Such systems can also contribute to predictive maintenance, identifying potential failures before they occur, thereby minimizing downtime and maintenance costs.
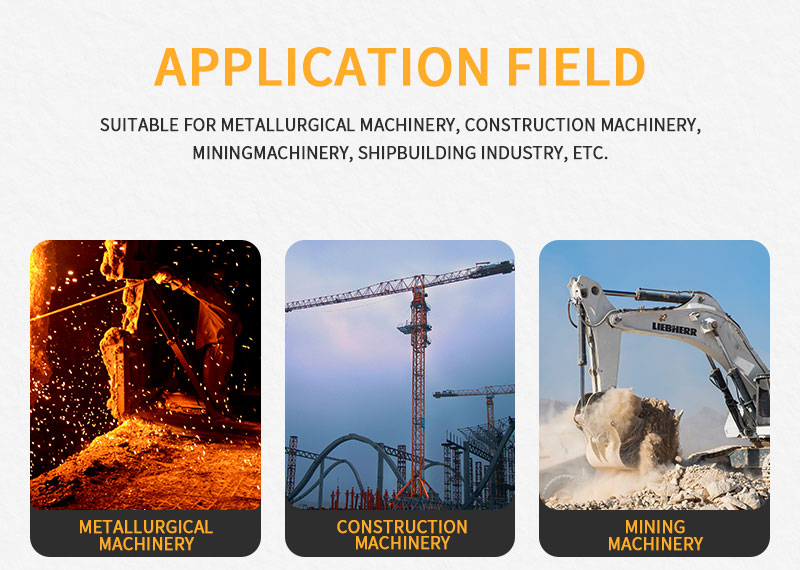
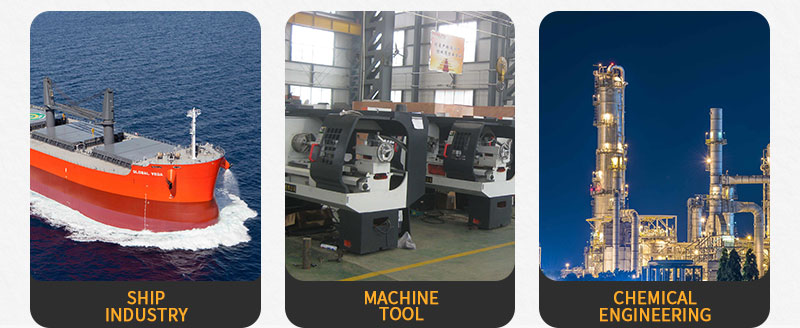