ERL100BRP2120NNN3S1NPA1NNNNNNNNNN danfoss pump
ERL100BRP2120NNN3S1NPA1NNNNNNNNNN danfoss pump

- Product Details
- Applicable Scene
Moreover, controlling the environmental conditions where the hydraulic system operates can also play a significant role in preventing contamination. If possible, keep hydraulic systems in clean, dust-free environments. Using dust covers, seals, and enclosures can protect hydraulic components from airborne particles that might enter the system.
ER-L-100B-RP-21-20-NN-N-3-S1NP-A1N-NNN-NNN-NNN
ERL100BRP2120NNN3S1NPA1NNNNNNNNNN
Monitoring system performance is essential for early detection of contamination issues. Implement pressure gauges, sensors, and alarms that can alert operators to potential problems such as pressure drops or abnormal readings. Early intervention can prevent more severe wear on the hydraulic pump and other components within the system.
83017428
Finally, consider the adoption of technology solutions such as online condition monitoring systems. These systems can provide real-time data on fluid quality and contamination levels, allowing for proactive maintenance actions. By integrating predictive maintenance strategies, operators can schedule maintenance based on actual system condition rather than relying on fixed intervals.
In conclusion, preventing hydraulic pump wear due to contamination in high-pressure systems requires a multifaceted approach. By implementing effective filtration, maintaining fluid cleanliness, ensuring proper handling and maintenance practices, designing systems mindfully, controlling environmental conditions, monitoring performance regularly, and utilizing advanced technology, operators can significantly extend the life of hydraulic components and improve system performance. Investing in these preventive measures not only enhances operational reliability but also reduces long-term maintenance costs.
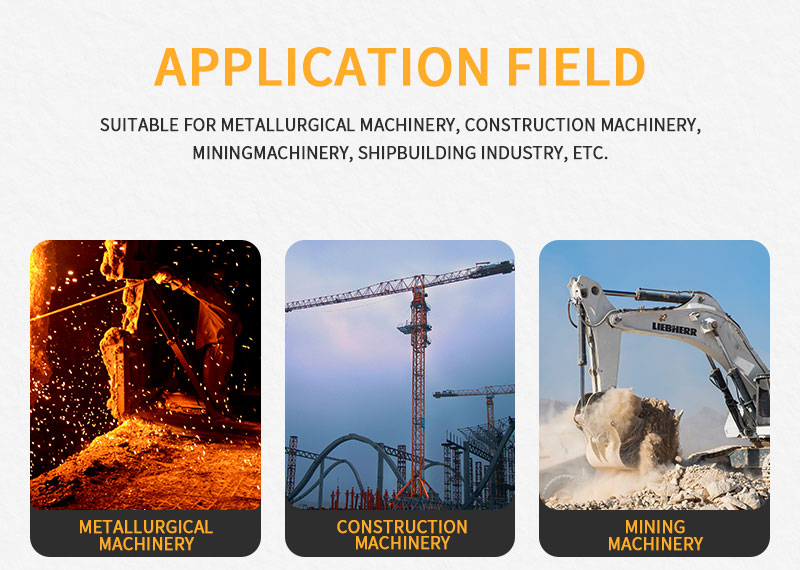
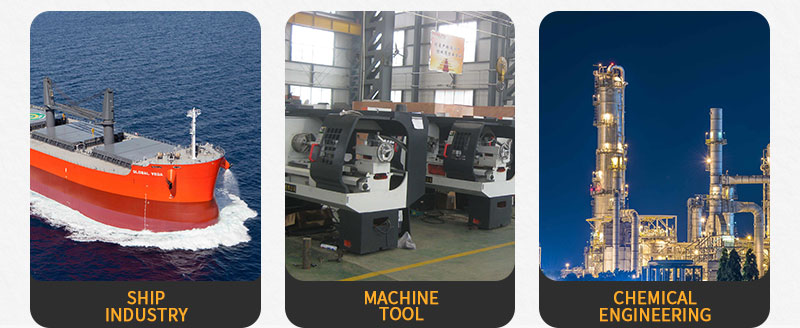