LRR025CRP1420NNN3C2NGA6NKNBNNNNNN piston pump
LRR025CRP1420NNN3C2NGA6NKNBNNNNNN piston pump

- Product Details
- Applicable Scene
In the aerospace industry, the integrity and performance of components are paramount. As the demands for safety and efficiency in air travel continue to grow, so does the need for rigorous testing procedures. One crucial tool in this landscape is the high-pressure pump, which plays an essential role in various testing processes for aerospace components.
LR-R-025C-RP-14-20-NN-N-3-C2NG-A6N-KNB-NNN-NNN
LRR025CRP1420NNN3C2NGA6NKNBNNNNNN
High-pressure pumps are designed to generate and maintain substantial hydraulic pressure, which is necessary for simulating the extreme conditions that aerospace components may face during operation. These pumps are used in several testing methodologies, including pressure endurance testing, leak testing, and functional testing. Each of these methods is vital for ensuring that components can withstand the harsh realities of flight.
7005203S
One of the primary applications of high-pressure pumps is in pressure endurance testing. This process involves subjecting components to pressures that exceed their maximum operational limits to evaluate their durability and failure points. For instance, fuel systems, hydraulic components, and structural parts are all tested to confirm that they can handle the extreme pressures encountered in various phases of flight. By using high-pressure pumps, engineers can gather critical data on how a component behaves under stress, allowing for design improvements and enhancing safety.
Another significant application is leak testing. High-pressure pumps can precisely pressurize a component or system and then monitor for any signs of leakage. Detecting leaks is vital in aerospace applications, as even the smallest leak in a fuel or hydraulic system can lead to catastrophic failures. Techniques such as pressure decay testing and bubble testing are employed, where a high-pressure pump supplies pressurized fluid to components, and engineers observe for any loss of pressure or formation of bubbles. These tests ensure that all components maintain integrity and meet stringent aerospace standards.
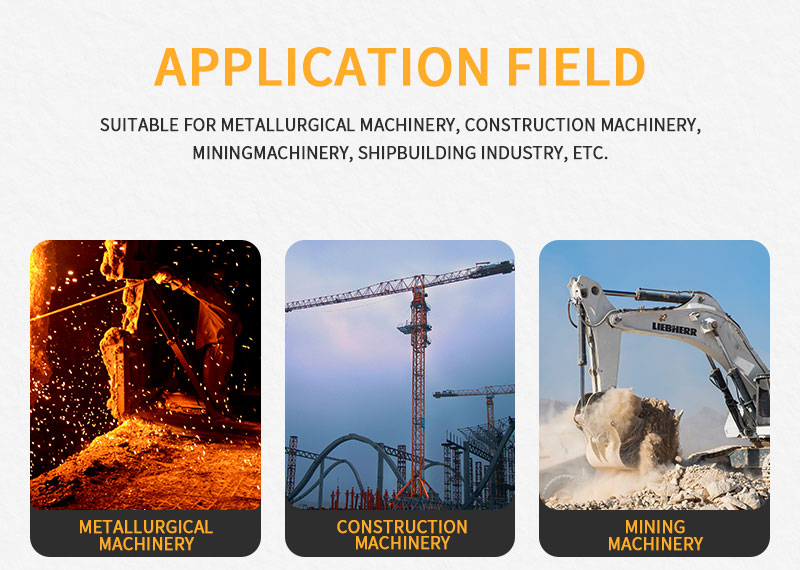
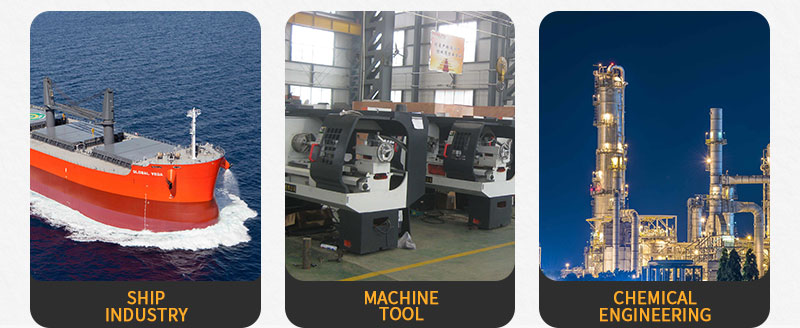