ERL100BLS2020NNN3S1APA1NNNNNNNNNN hydraulic oil pump
ERL100BLS2020NNN3S1APA1NNNNNNNNNN hydraulic oil pump

- Product Details
- Applicable Scene
Hydraulic pumps are critical components in fluid systems for power generation units, enabling the efficient transfer of energy and ensuring the smooth operation of various machinery. However, failures in hydraulic pumps can lead to significant downtime, costly repairs, and compromised system efficiency. To avoid these issues, implementing preventative measures is essential. Here are several strategies to prevent hydraulic pump failures in fluid systems.
ER-L-100B-LS-20-20-NN-N-3-S1AP-A1N-NNN-NNN-NNN
ERL100BLS2020NNN3S1APA1NNNNNNNNNN
Regular Maintenance and Inspection
80006660
Routine maintenance is the cornerstone of preventing hydraulic pump failures. Establish a regular inspection schedule to check for signs of wear and tear, leaks, and unusual noises. Key components such as seals, O-rings, and bearings should be examined and replaced as needed. Additionally, monitoring fluid levels and conditions can help identify potential problems before they escalate.
Proper Fluid Selection
Using the correct hydraulic fluid is crucial for optimal pump performance. The fluid should meet the manufacturer’s specifications and be appropriate for the operating conditions, including temperature and pressure ranges. Regularly testing the fluid for contamination, viscosity, and water content can also ensure that it remains within acceptable limits. Contaminated or degraded fluid can lead to increased wear and pump failure.
Contamination Control
Contamination is one of the leading causes of hydraulic pump failure. Particulate matter, water, and air can significantly disrupt system performance. Implementing proper filtration and separation systems can help minimize contamination risks. Regularly changing filters and ensuring that all components are properly cleaned can substantially reduce the likelihood of pump failure.
Monitoring System Parameters
Utilizing condition monitoring technologies can be instrumental in preventing hydraulic pump failures. Data such as temperature, pressure, and flow rates should be continuously monitored. Sudden deviations from normal operating ranges can indicate potential issues. By identifying trends and anomalies early, operators can take corrective actions before a failure occurs.
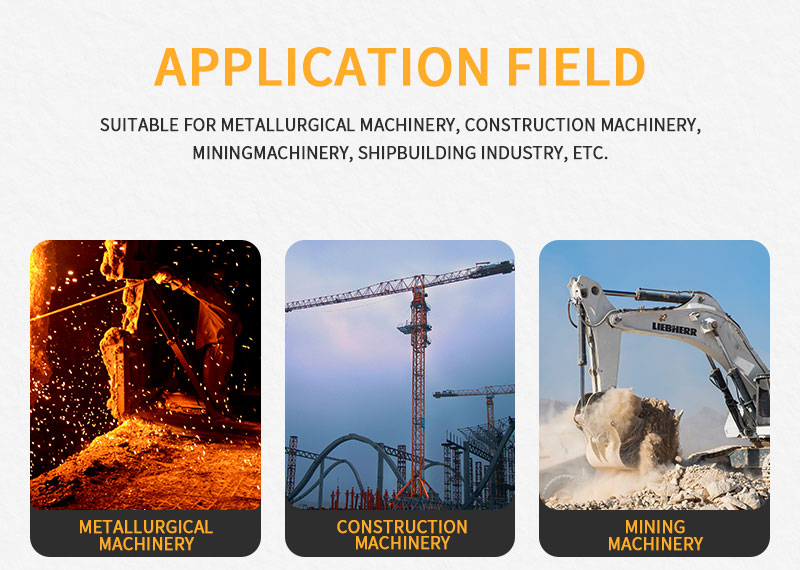
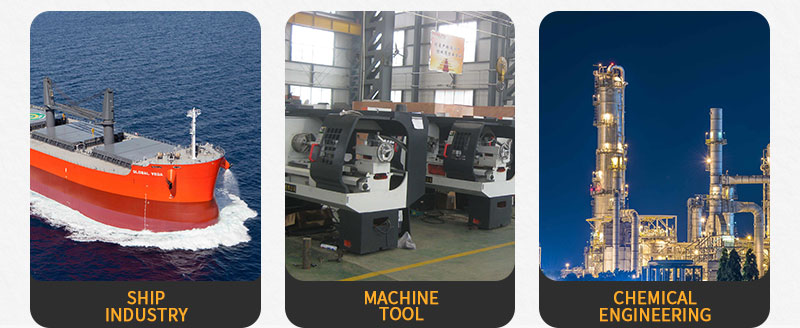