90L100KP1AB60P3S1E00GBA383824 hydraulic pump
90L100KP1AB60P3S1E00GBA383824 hydraulic pump

- Product Details
- Applicable Scene
Precision casting processes are essential in various manufacturing industries, providing components with exceptional accuracy and surface finish. One of the critical technologies that enhance these processes is the plunger pump. By understanding how plunger pumps operate and their significant contributions to precision casting, we can appreciate their role in improving product quality and production efficiency.
90-L-100-KP-1-AB-60-P-3-S1-E-00-GBA-38-38-24
90L100KP1AB60P3S1E00GBA383824
Plunger pumps are positive displacement pumps that utilize a reciprocating plunger to move fluids through a cylinder. They are characterized by their ability to generate high pressure and deliver precise volumes of liquid. In the context of precision casting, these pumps are particularly valuable for several reasons.
83049590
First and foremost, plunger pumps offer precise control over the flow rate of molten materials. In precision casting, achieving the correct fluid dynamics is crucial for filling molds uniformly and avoiding defects such as air pockets or incomplete fills. By providing consistent flow rates, plunger pumps ensure that the molten metal or alloy is delivered uniformly and at the right pressure, which is vital for maintaining the integrity of the cast product.
Moreover, the ability to control the injection speed and pressure of the material being cast is another advantage of using plunger pumps. These pumps can be adjusted to vary the speed of the plunger movement, enabling manufacturers to optimize the filling process for different types of molds and materials. This flexibility minimizes the risk of turbulence and allows for a smoother casting operation, which ultimately contributes to better surface finishes and dimensional accuracy.
Another significant benefit of plunger pumps in precision casting is their reliability in maintaining consistent operating conditions. The design of plunger pumps allows for minimal variation in performance, which is essential when dealing with high-temperature molten metals. This reliability means that manufacturers can achieve repeatable results over multiple casting cycles, enhancing productivity and reducing waste due to defects.
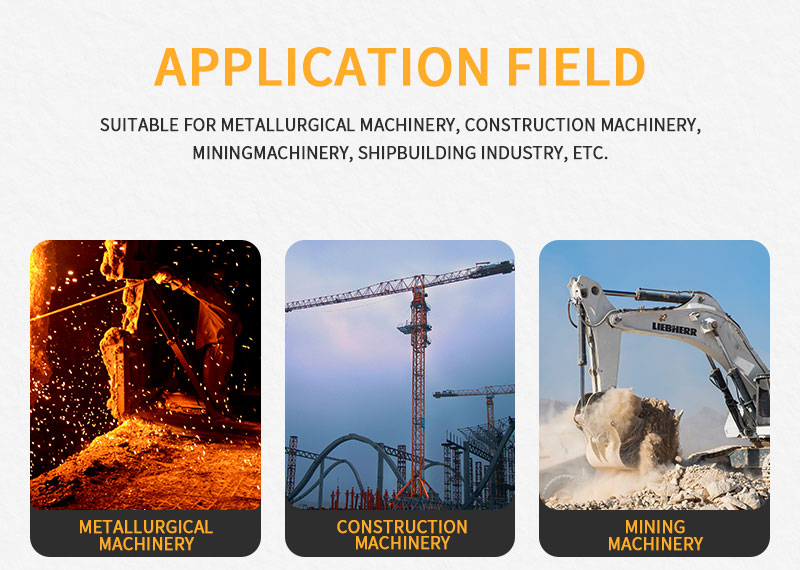
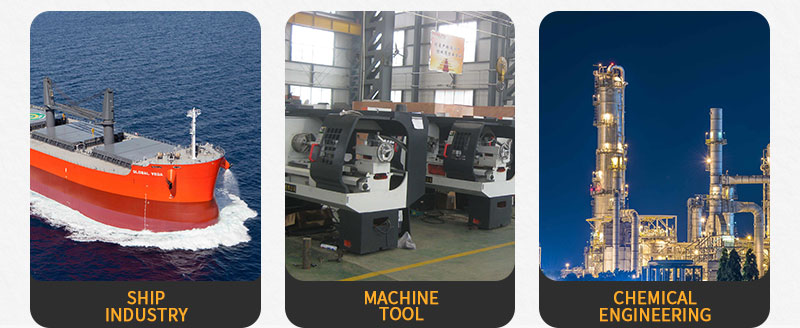