90R075HF5CD80S3C6D03GBA424224 piston pump
90R075HF5CD80S3C6D03GBA424224 piston pump

- Product Details
- Applicable Scene
Hydraulic pumps play a crucial role in various industries, from manufacturing to aerospace, by providing the necessary hydraulic power to operate machinery and equipment. In experimental testing and prototyping, these pumps are indispensable for validating designs, optimizing performance, and ensuring reliability. This article explores the importance of hydraulic pumps in these processes and highlights best practices for their efficient use.
90R075-HF-5-CD-80-S-3-C6-D-03-GBA-42-42-24
90R075HF5CD80S3C6D03GBA424224
The primary function of a hydraulic pump is to convert mechanical energy into hydraulic energy. This transformation is accomplished through the movement of hydraulic fluids, enabling machines to carry out tasks such as lifting, pressing, and rotating. In experimental testing and prototyping, hydraulic pumps serve as essential components of the hydraulic circuits that simulate real-world operating conditions, allowing engineers to evaluate system performance and identify potential issues before full-scale production.
80002504
One of the significant advantages of using hydraulic systems in prototyping is their ability to generate high force outputs in a compact configuration. This quality is especially beneficial when testing scalable designs or creating prototypes of complex machinery where space constraints are a concern. By utilizing hydraulic pumps, engineers can achieve precise control over fluid flow and pressure, facilitating accurate measurements and effective stress testing of prototypes.
During the experimental testing phase, the selection of the appropriate hydraulic pump is critical. Factors such as flow rate, pressure range, and efficiency must be considered to match the specific requirements of the project. Variable displacement pumps, for example, offer the flexibility to adjust output based on load demands, making them suitable for dynamic testing environments. On the other hand, positive displacement pumps can provide consistent flow for more stable testing scenarios.
In addition to choosing the right pump, proper setup and calibration are vital for achieving accurate test results. Calibration ensures that the hydraulic system functions within desired parameters, allowing engineers to trust the data collected during experiments. Regular maintenance and inspections of hydraulic pumps are also essential to prevent failures and ensure continuous operation throughout testing processes.
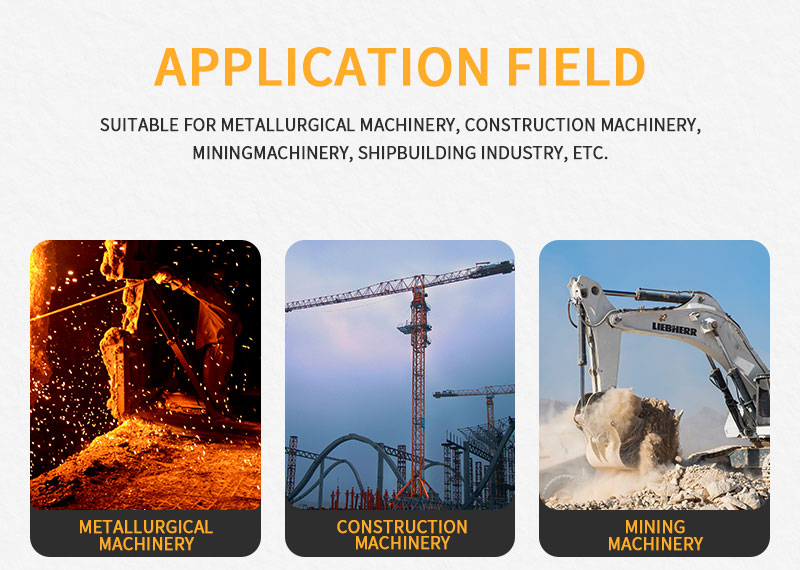
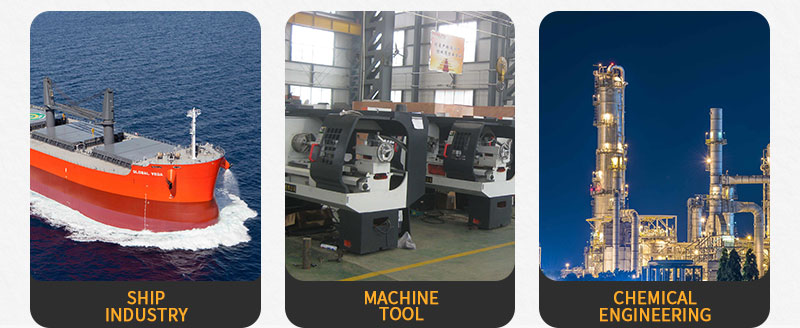