KRR045DLS1420NNN3C2BRA6NAAANNNNNN sauer danfoss pump
KRR045DLS1420NNN3C2BRA6NAAANNNNNN sauer danfoss pump

- Product Details
- Applicable Scene
Hydraulic systems play a critical role in modern aviation, powering everything from landing gear to flight control surfaces. At the heart of these systems lies the hydraulic oil pump, responsible for generating and maintaining the necessary hydraulic pressure. Designing hydraulic oil pumps for aircraft hydraulic actuators and control surfaces involves a comprehensive understanding of engineering principles, material selection, and regulatory compliance.
KR-R-045D-LS-14-20-NN-N-3-C2BR-A6N-AAA-NNN-NNN
KRR045DLS1420NNN3C2BRA6NAAANNNNNN
The primary function of hydraulic oil pumps in aircraft is to convert mechanical energy into hydraulic energy. This process involves drawing hydraulic fluid from a reservoir and pressurizing it to create fluid flow, which is then transmitted to various actuators that control pivotal components like flaps, slats, and ailerons. Therefore, the design of these pumps needs to consider several critical aspects.
83046719
One of the foremost aspects is the pump’s flow rate and pressure output. Aircraft systems require high reliability and performance under various operational conditions. For instance, pumps must be capable of delivering enough fluid volume to accommodate rapid movements of control surfaces during critical phases like takeoff and landing. Engineers use advanced simulation tools to predict flow characteristics and performance under simulated conditions of pressure and temperature fluctuations that can occur during flight.
Material selection is another critical factor in pump design. Given the harsh operational environments experienced by aircraft—including significant temperature variations, exposure to corrosive hydraulic fluids, and high stress—the materials used in the construction of hydraulic pumps must exhibit high strength and excellent resistance to wear and corrosion. Lightweight materials, such as aluminum alloys and composite materials, are often preferred to maintain the overall weight of the aircraft while ensuring that the pumps can perform reliably.
Moreover, hydraulic oil pumps must be designed with a focus on operational efficiency. This includes minimizing energy loss through friction and optimizing the pump’s geometry to ensure smooth flow. Advanced computational fluid dynamics (CFD) techniques allow engineers to model and analyze flow patterns, leading to enhancements in pump design that can improve efficiency and reduce noise during operation.
Safety and regulatory compliance are paramount in the aerospace industry. Hydraulic oil pumps must adhere to stringent standards set by aviation authorities, such as the Federal Aviation Administration (FAA) and the European Union Aviation Safety Agency (EASA). This includes rigorous testing and validation procedures to ensure the pumps can withstand various failure modes, including leakages, mechanical failures, and extreme pressure scenarios. Robust testing not only confirms compliance but also enhances the pump design by identifying areas for improvement.
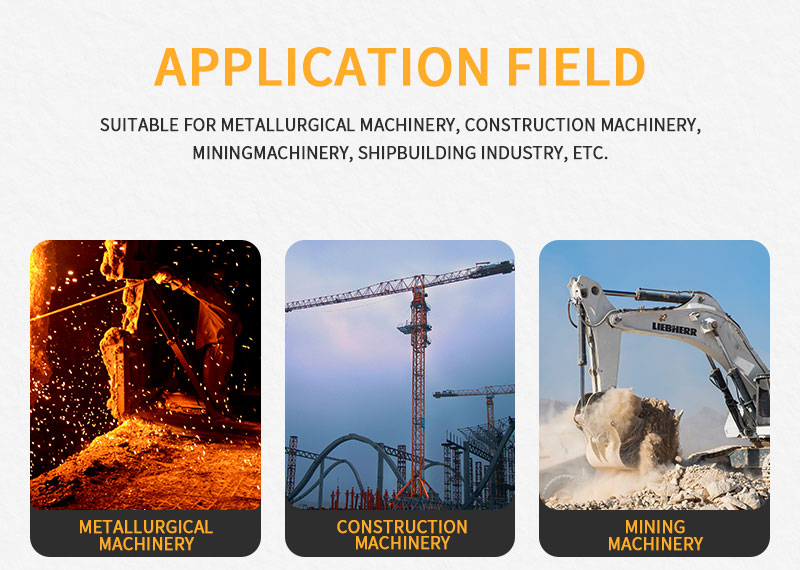
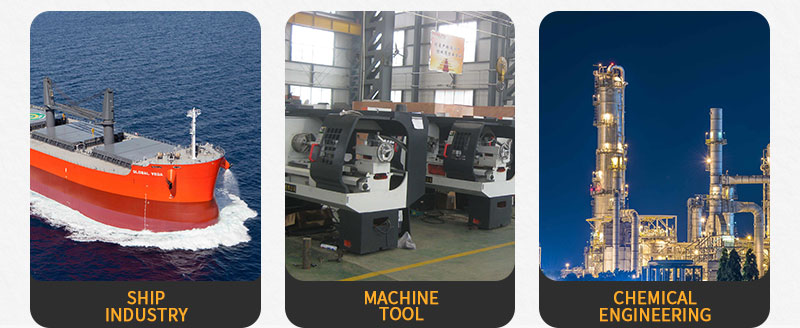