90L075KA5NN80S3S1E03GBA303028 piston pump
90L075KA5NN80S3S1E03GBA303028 piston pump

- Product Details
- Applicable Scene
In the evolving landscape of manufacturing, digital twins have emerged as a powerful tool for optimizing processes and enhancing operational efficiency. Among various equipment types, hydraulic oil pumps play a critical role in many industrial applications. Their integration into digital twin systems not only helps in monitoring performance but also facilitates predictive maintenance and optimization strategies, ultimately leading to increased productivity and reduced costs.
90L075-KA-5-NN-80-S-3-S1-E-03-GBA-30-30-28
90L075KA5NN80S3S1E03GBA303028
Digital twins are virtual replicas of physical systems. They utilize real-time data from sensors embedded in equipment, allowing manufacturers to simulate operations and monitor performance remotely. By integrating hydraulic oil pumps into these digital twin environments, manufacturers gain valuable insights into the functioning of their hydraulic systems, helping them make data-driven decisions.
83015050
One of the primary benefits of integrating hydraulic oil pumps into digital twins is the ability to monitor real-time performance. Sensors can measure parameters such as pressure, flow rate, and temperature, sending data back to the digital twin. This continuous stream of information allows manufacturers to identify anomalies and inefficiencies quickly. For example, if a hydraulic oil pump is operating outside its optimal pressure range, the digital twin can alert operators to the potential issue before it results in equipment failure or downtime.
Predictive maintenance is another significant advantage of this integration. By analyzing historical data and real-time performance metrics, manufacturers can develop predictive models that forecast when maintenance should be performed. This approach limits unnecessary downtime and reduces maintenance costs. Instead of adhering to a rigid maintenance schedule, operators can address issues based on actual pump conditions, thus enhancing equipment longevity and reliability.
Moreover, digital twins can assist in optimizing the configuration and operation of hydraulic systems. By simulating various scenarios within the virtual environment, manufacturers can test different settings and configurations to determine the most efficient operating conditions. For example, a digital twin can help identify an optimal pump speed or sequence of operations that maximizes efficiency while minimizing energy consumption.
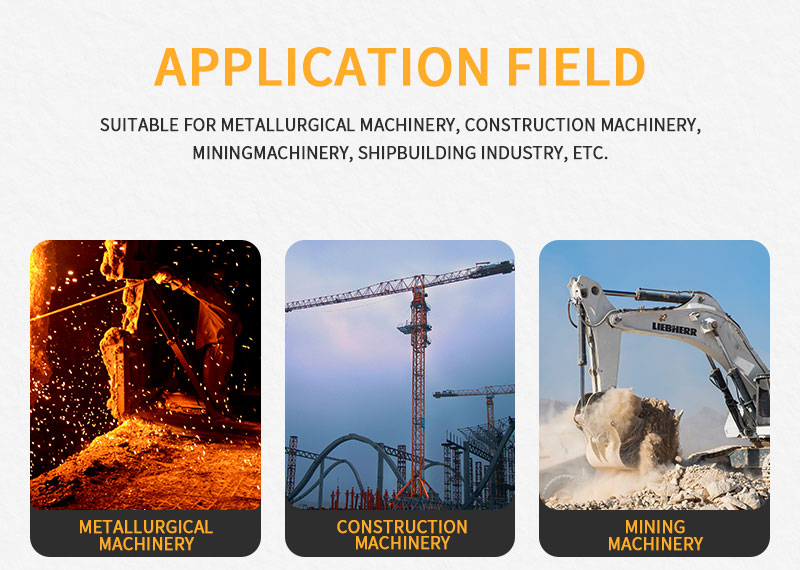
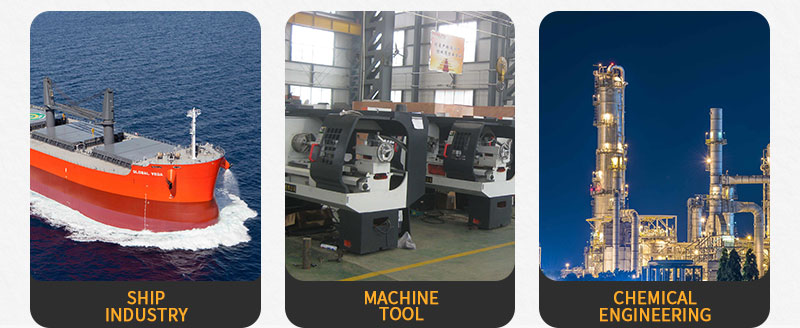