ERL100BLB2120NNN3S2APA1NAAANNNNNN hydraulic pump
ERL100BLB2120NNN3S2APA1NAAANNNNNN hydraulic pump

- Product Details
- Applicable Scene
Plunger pumps play a crucial role in various industrial applications, particularly in high-risk environments where safety and efficiency are paramount. These pumps are known for their ability to handle viscous fluids and high-pressure operations, making them ideal for sectors such as oil and gas, chemical processing, and water treatment. However, the critical nature of their use also means that regular inspection and maintenance are essential to prevent catastrophic failures. This article explores the importance of plunger pump inspection in high-risk environments, emphasizing safety, reliability, and operational efficiency.
ER-L-100B-LB-21-20-NN-N-3-S2AP-A1N-AAA-NNN-NNN
ERL100BLB2120NNN3S2APA1NAAANNNNNN
One of the foremost reasons for conducting regular inspections of plunger pumps in high-risk environments is safety. Failures in pumps can lead to severe accidents, including leaks of hazardous materials, explosions, or fires, which could endanger workers and cause significant environmental damage. Regular inspections help identify wear and tear, misalignments, or material fatigue before they escalate into critical failures. By addressing these issues proactively, companies can mitigate risks and create a safer workplace for their employees.
7000539
Moreover, the reliability of plunger pumps is crucial for maintaining operational continuity. In industries that are time-sensitive and require constant flow, such as oil extraction and chemical manufacturing, a sudden pump failure can lead to costly downtime. Inspections allow for the early detection of potential issues, enabling organizations to schedule maintenance during non-peak hours or routine shut-downs rather than facing unexpected failures. This proactive approach ensures a steady flow of production and prevents financial losses associated with unplanned repairs.
Another significant factor to consider is the impact of inspections on operational efficiency. Over time, plunger pumps can lose their efficiency due to wear and tear, leading to increased energy consumption and operating costs. Regular inspections not only help maintain the pumps’ operational integrity but also allow for the optimization of performance. By keeping the pumps in top shape, companies can achieve better fuel efficiency and lower operational costs, contributing to overall productivity.
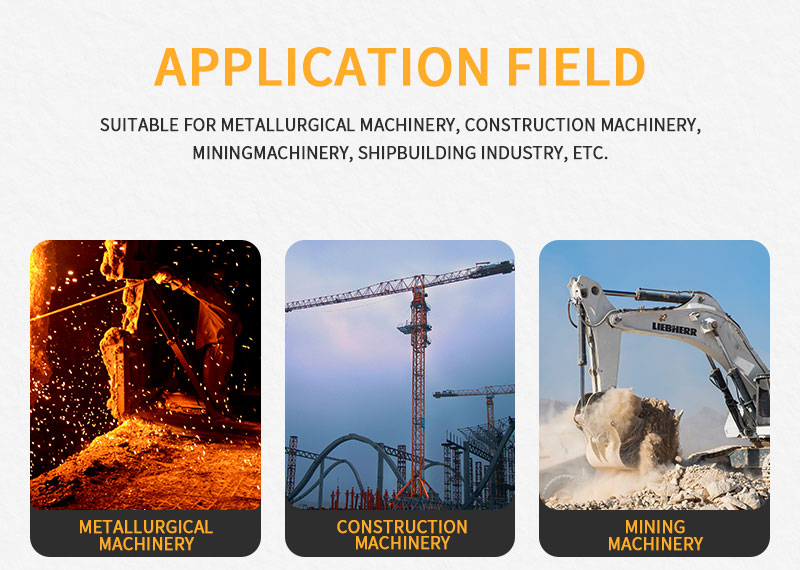
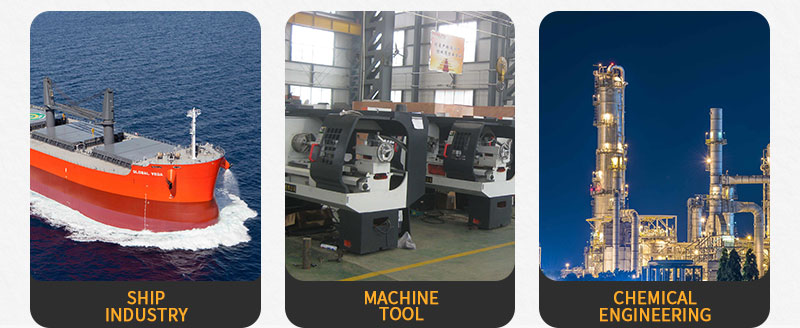