ERL130BPC25NNNNN3S1NPA1NNNNNNNNNN sauer danfoss pump
ERL130BPC25NNNNN3S1NPA1NNNNNNNNNN sauer danfoss pump

- Product Details
- Applicable Scene
Cavitation in hydraulic pumps can lead to severe operational issues in fluid circuits, particularly within power plant systems. This phenomenon occurs when the pressure in the fluid drops below its vapor pressure, causing the formation of vapor bubbles that can collapse violently, leading to damage to the pump and associated equipment. Addressing cavitation is critical for maintaining efficiency, safety, and longevity of hydraulic systems. Here is a comprehensive approach to solving hydraulic pump cavitation in fluid circuits for power plant systems.
ER-L-130B-PC-25-NN-NN-N-3-S1NP-A1N-NNN-NNN-NNN
ERL130BPC25NNNNN3S1NPA1NNNNNNNNNN
Understanding Cavitation
83011634
Cavitation is primarily caused by low pressure at the pump inlet or high temperature of the fluid. It often occurs due to flow restrictions, inadequate pump sizing, or improper system design. Recognizing the conditions that lead to cavitation can help in implementing effective solutions.
Analyze System Design
Begin by reviewing the existing hydraulic circuit design. Check for bends, fittings, and restrictions that might cause excessive pressure drops. Streamlining the system by minimizing sharp turns and using appropriately sized piping can help maintain a stable flow and pressure, reducing the likelihood of cavitation.
Pump Sizing and Selection
Ensure that the pump is correctly sized for the application. Pumps that are too small or not appropriately matched to the system can induce conditions favorable for cavitation. Consult manufacturer specifications and consider factors such as flow rate, pressure characteristics, and the specific gravity of the fluid.
Maintain Inlet Conditions
Improving the inlet conditions can significantly reduce cavitation risks. This can be achieved by:
Ensuring that the pump has a proper suction head. Elevating the pump or installing a booster pump may help maintain adequate pressure.
Maintaining the fluid temperature within acceptable limits. Consider cooling solutions or heat exchangers to stabilize fluid temperatures, especially in high-temperature applications.
Installing larger suction pipe diameters to lower fluid velocity and reduce pressure drops.
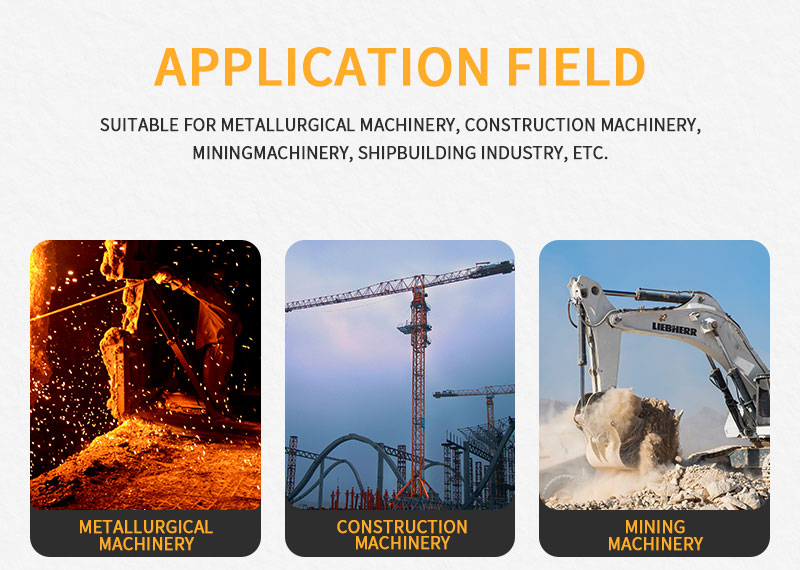
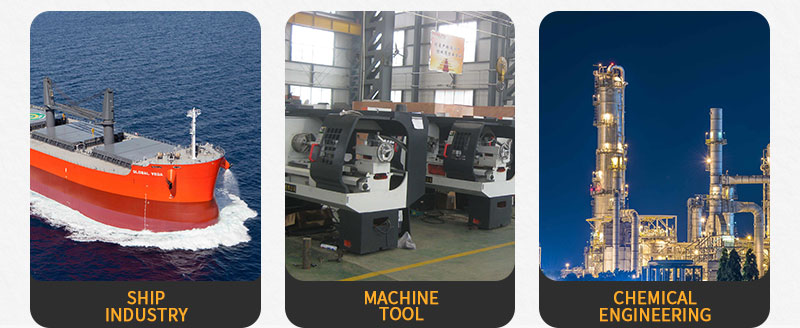