90L180KA1NN80TCF1J03FAC292924 high pressure pump
90L180KA1NN80TCF1J03FAC292924 high pressure pump

- Product Details
- Applicable Scene
Hydraulic pumps are essential components in various machinery, especially in high-torque applications where significant force is required. However, these pumps can experience performance loss due to several factors, impacting operational efficiency and machine longevity. Understanding and addressing these issues is crucial for maintaining optimal performance. Here, we explore common causes of hydraulic pump performance loss and effective solutions.
90-L-180-KA-1-NN-80-T-C-F1-J-03-FAC-29-29-24
90L180KA1NN80TCF1J03FAC292924
One of the primary reasons for performance loss in hydraulic pumps is wear and tear on internal components. High-torque applications place immense stress on these components, leading to erosion and fatigue. Regular maintenance is critical; operators should implement a scheduled inspection plan to identify and replace worn parts before they cause significant issues. Using high-quality, compatible hydraulic fluids can also minimize wear, ensuring smoother operation.
9820159
Another common issue is cavitation, which occurs when there is insufficient pressure at the pump inlet. This leads to the formation of vapor bubbles, which can collapse violently and damage the pump. To combat cavitation, ensure that the hydraulic system is properly designed with adequate fluid levels and that the pump is located close to the oil reservoir. Additionally, maintaining proper fluid viscosity and temperature can help prevent cavitation.
Fluid contamination is another significant factor affecting hydraulic pump performance. Contaminants such as dirt, water, or air can degrade fluid quality, causing efficiency loss and accelerating wear. Implementing strict filtration systems and regularly monitoring fluid quality will help keep contaminants at bay. Operators should also maintain proper seals and connections to prevent leaks and ingress of contaminants into the system.
Overheating is a critical concern in high-torque applications, often caused by excessive load or inadequate cooling. Over time, elevated temperatures can lead to fluid breakdown, reducing lubrication properties and accelerating wear. To mitigate overheating, it is essential to ensure the hydraulic system is properly sized for the application and equipped with an efficient cooling system. Regular monitoring of temperature can help identify overheating issues before they lead to severe damage.
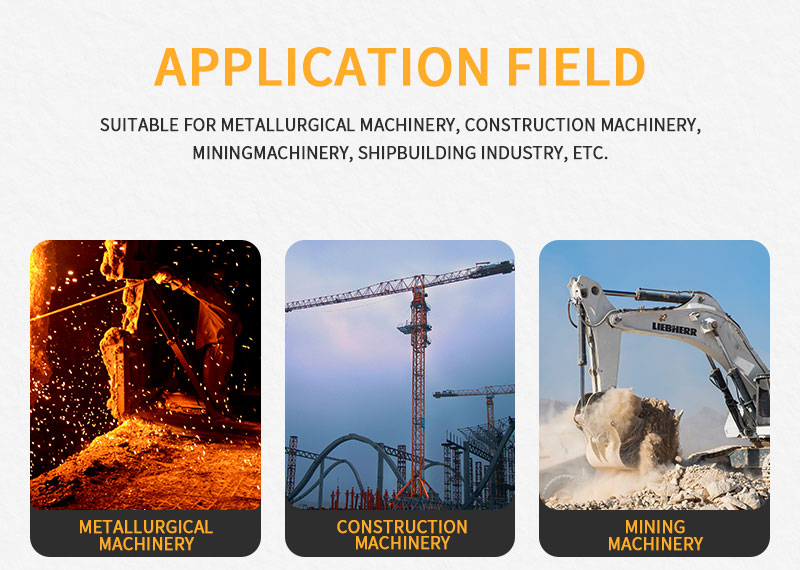
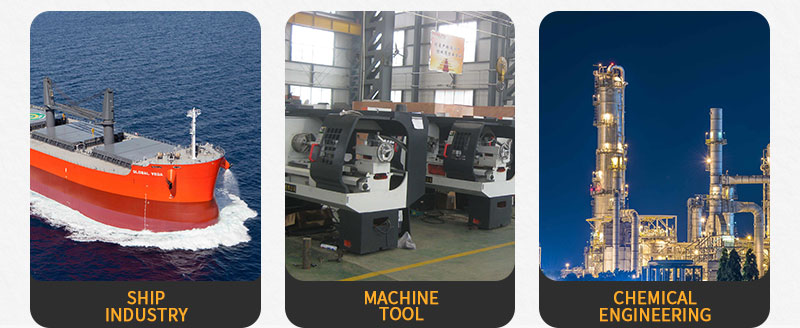