KRR045DPC21NNNNN3K2NFA6NPLBNNNNNN piston pump
KRR045DPC21NNNNN3K2NFA6NPLBNNNNNN piston pump

- Product Details
- Applicable Scene
In the manufacturing industry, overhead cranes play a critical role in material handling, enabling the efficient movement of heavy loads within production facilities. One of the essential components that contribute to the smooth operation of these cranes is the hydraulic oil pump. Designing hydraulic oil pumps specifically for overhead cranes requires a comprehensive understanding of their operational needs, system specifications, and environmental considerations.
KR-R-045D-PC-21-NN-NN-N-3-K2NF-A6N-PLB-NNN-NNN
KRR045DPC21NNNNN3K2NFA6NPLBNNNNNN
Hydraulic oil pumps convert mechanical energy into hydraulic energy by pressurizing hydraulic fluid, which is then used to power the crane’s lifting mechanisms. When designing these pumps, several key factors must be taken into account to ensure optimal performance, reliability, and safety.
7004188S
First and foremost is the load capacity. Overhead cranes in manufacturing plants often handle substantial weights, so the hydraulic pump must be capable of generating sufficient pressure to lift these loads safely. The design should consider peak load requirements, as well as dynamic forces caused by acceleration, deceleration, and the occasional shock loading due to sudden changes in movement.
Another essential aspect is the pump type. The most common types of hydraulic pumps used in overhead cranes are gear pumps, vane pumps, and piston pumps. Gear pumps are known for their simplicity and durability, making them suitable for applications requiring high flow rates at relatively low pressures. Vane pumps, while less common, can offer variable flow rates and are efficient under varying load conditions. Piston pumps, although more complex, provide high pressure capabilities, making them ideal for heavy-duty applications.
Efficiency is a critical consideration when designing hydraulic pumps. A pump that operates efficiently minimizes energy consumption and reduces operational costs. This can be achieved through careful selection of pump components, such as optimizing the rotor and stator design in gear pumps or ensuring precision tolerances in piston pumps.
Moreover, reliability and maintenance are vital factors. Hydraulic systems are often subject to wear and tear due to high pressures and fluid dynamics. Thus, the pump design must incorporate features that enhance durability, such as using high-quality materials that resist corrosion and wear. Additionally, designing for ease of maintenance—like providing accessible inspection points and modular components for quick replacement—can significantly reduce downtime and prolong the overall lifespan of the cranes.
Temperature control is another aspect that cannot be overlooked. Hydraulic fluids can degrade or lose viscosity at extreme temperatures, leading to reduced efficiency and potential pump failure. Implementing cooling systems and using fluids with a suitable temperature range are essential strategies for maintaining optimal performance.
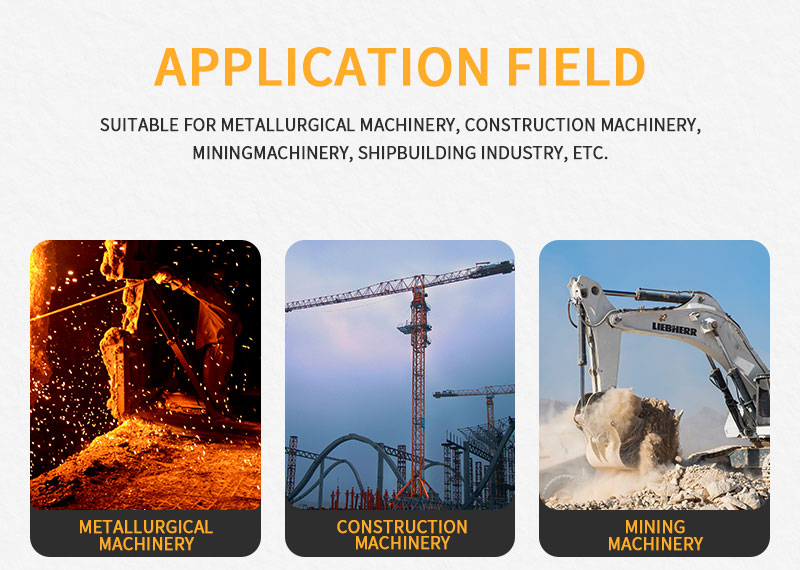
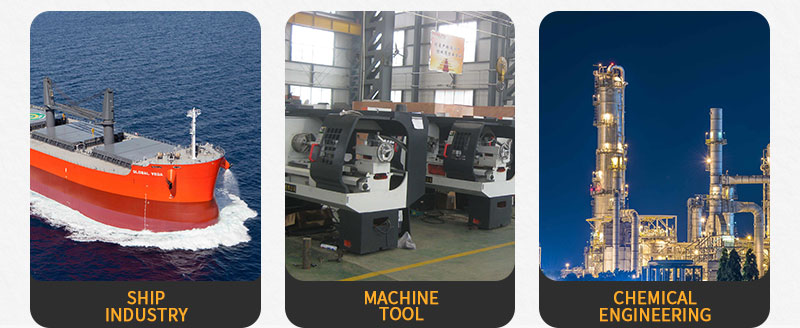