90L180HS5BC80TCF1J03FAC424228 sauer danfoss pump
90L180HS5BC80TCF1J03FAC424228 sauer danfoss pump

- Product Details
- Applicable Scene
Cavitation in hydraulic pumps can be a significant issue in precision fluid circulation systems, leading to reduced efficiency, noise, and potential damage to components. Understanding and addressing cavitation is essential for the longevity and performance of hydraulic systems. This article explores the causes of cavitation, its effects, and effective solutions to mitigate the problem.
90-L-180-HS-5-BC-80-T-C-F1-J-03-FAC-42-42-28
90L180HS5BC80TCF1J03FAC424228
Cavitation occurs when the pressure of the fluid falls below its vapor pressure, leading to the formation of vapor bubbles. When these bubbles travel to areas of higher pressure, they collapse violently, causing shock waves that can damage pump components and reduce overall performance. The primary causes of cavitation in hydraulic systems include:
83018113
Low Fluid Pressure: Insufficient inlet pressure can be a critical factor for cavitation. If the pressure at the pump intake is too low, it can easily drop below the fluid’s vapor pressure.
High Fluid Temperature: Increased fluid temperature reduces the viscosity and increases vapor pressure, making cavitation more likely under certain operational conditions.
High Flow Resistance: Blockages or restrictions in the system—such as bends, valves, or filters—can increase localized pressure drops, creating conditions conducive to cavitation.
Pump Design: Inadequate pump design for specific applications, including factors like cavitation margin and Net Positive Suction Head (NPSH), can leave systems more susceptible to cavitation.
To solve hydraulic pump cavitation problems, several strategies can be employed:
Increase Inlet Pressure: Always ensure that the pump receives sufficient inlet pressure, either by using a pressurized feed tank or by reducing the distance from the tank to the pump.
Reduce Fluid Temperature: Employ cooling mechanisms if the fluid temperature is above optimal levels. This can involve using heat exchangers or selecting fluids with lower vapor pressures.
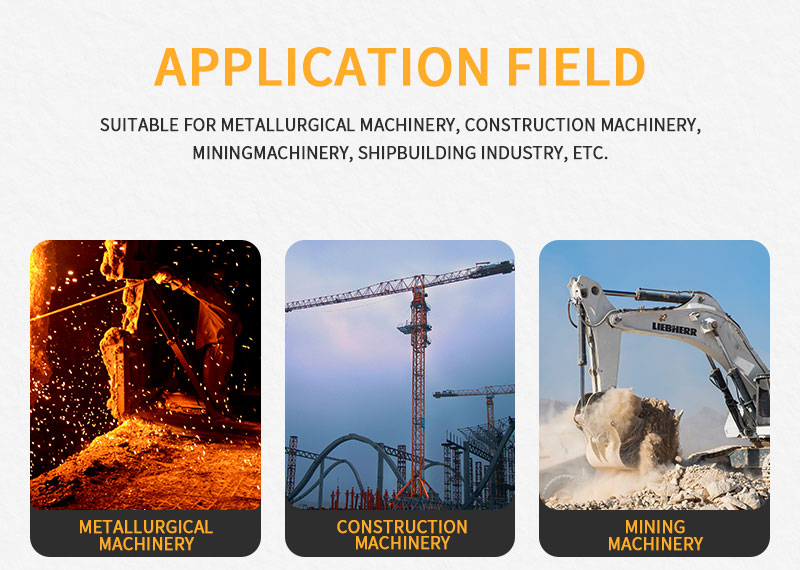
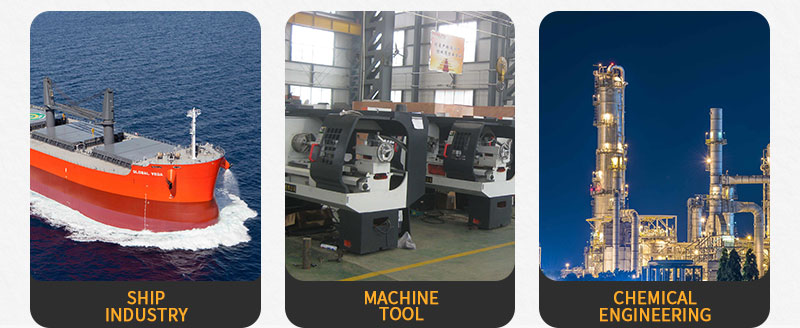