FRR074BLS2215NNN3S1N4A1NNNNNNNNNN piston pump
FRR074BLS2215NNN3S1N4A1NNNNNNNNNN piston pump

- Product Details
- Applicable Scene
In the aerospace industry, where precision and reliability are paramount, the ability to simulate high-pressure environments is crucial for testing components under conditions they will face in real-world applications. Danfoss Pumps have emerged as key players in this domain, providing innovative solutions that facilitate the rigorous testing needed for aerospace components.
FR-R-074B-LS-22-15-NN-N-3-S1N4-A1N-NNN-NNN-NNN
FRR074BLS2215NNN3S1N4A1NNNNNNNNNN
Danfoss is renowned for its advanced hydraulic solutions, and its pumps are specifically designed to handle high pressures while ensuring a steady flow of fluids. This capability makes them ideal for creating controlled environments necessary for testing aerospace components, which must withstand extreme conditions such as those found during take-off, flight, and landing.
7002515
One of the primary applications of Danfoss pumps in aerospace testing is in the simulation of hydraulic systems. Aircraft rely heavily on hydraulic systems for various functions, including landing gear operation, flight control actuation, and overall system integrity. By using Danfoss pumps, engineers can replicate the high-pressure hydraulic conditions that these components experience, providing valuable insights into their performance and reliability.
The robustness of Danfoss pumps allows for a wide range of fluid viscosities, enabling the simulation of different operational conditions. This versatility is essential in aerospace testing, as components may encounter various fluids under different temperatures and pressures. By adjusting the parameters of the pump, engineers can conduct comprehensive tests that emulate a broad spectrum of real-life scenarios.
Furthermore, the precision engineering of Danfoss pumps ensures that the simulations are not only accurate but also repeatable. Consistency in testing is vital for regulatory compliance and for ensuring that components meet stringent safety and performance standards. The ability to produce the same conditions multiple times allows for effective validation of design assumptions and performance metrics.
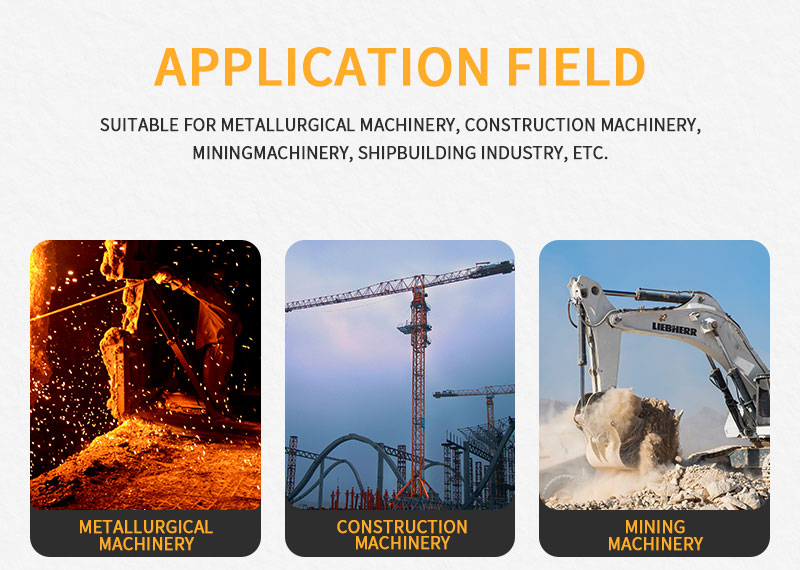
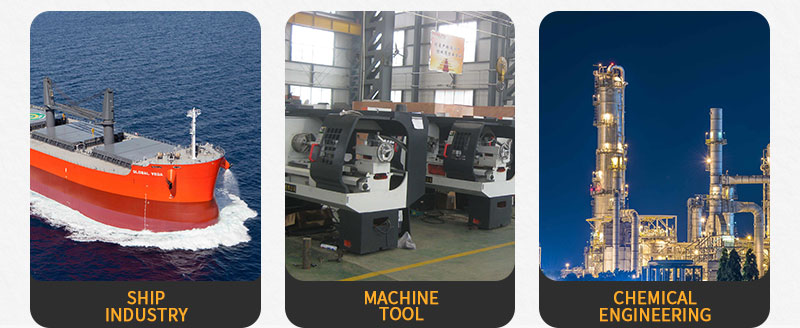