ERR100BLS1820NNN3S1CPA1NAAANNNNNN hydraulic pump
ERR100BLS1820NNN3S1CPA1NAAANNNNNN hydraulic pump

- Product Details
- Applicable Scene
Poor installation practices can result in misalignment, leading to uneven wear or stress on seals. It is imperative to ensure that seals are installed correctly, following the manufacturer’s specifications. Training maintenance personnel on proper installation techniques and using alignment tools can prevent these issues from arising.
ER-R-100B-LS-18-20-NN-N-3-S1CP-A1N-AAA-NNN-NNN
ERR100BLS1820NNN3S1CPA1NAAANNNNNN
Material compatibility is another crucial aspect to consider. Selecting the right seal material that is compatible with the hydraulic fluid, pressure, and temperature conditions is essential. Working closely with suppliers to choose seals that meet specific operational requirements can minimize the likelihood of failure.
83040005
If a seal failure does occur, prompt action is critical. First, identify the cause of the failure by inspecting the seal and surrounding components. Look for signs of wear, contamination, or misalignment. Once the root cause is established, replace the faulty seals with new, compatible materials. It is also vital to address any underlying issues, such as system pressure or contamination, to prevent future failures.
In summary, effectively solving hydraulic pump seal failures in high-pressure systems involves a comprehensive understanding of potential causes and implementing proactive measures. By monitoring system conditions, ensuring correct installation, selecting appropriate materials, and addressing any issues promptly, companies can significantly reduce the risk of seal failures, enhance the longevity of hydraulic systems, and maintain optimal operational efficiency. Regular maintenance and attention to detail are key to achieving these goals and ensuring the reliability of high-pressure hydraulic systems.
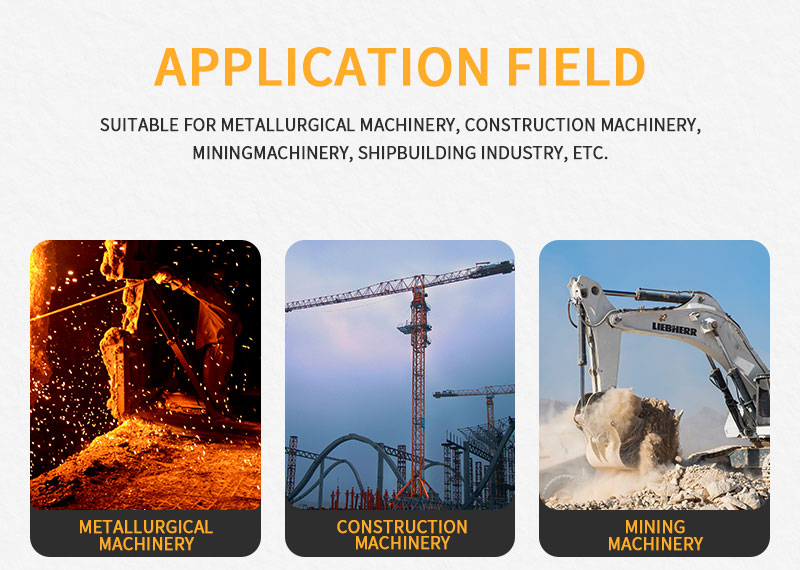
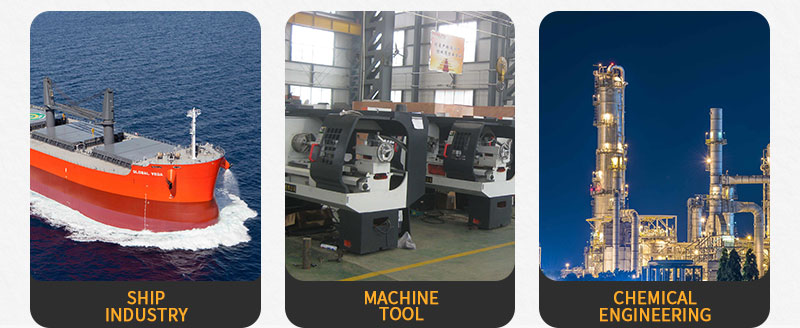