FRL074BPC25NNNNN3S1N2A1NAAANNNNNN danfoss pump
FRL074BPC25NNNNN3S1N2A1NAAANNNNNN danfoss pump

- Product Details
- Applicable Scene
Piston pumps are integral components in fluid power systems, widely used for their efficiency, reliability, and adaptability in various applications. These pumps convert mechanical energy into hydraulic energy, creating fluid flow and pressure suitable for transferring power to hydraulic machinery. This article explores the design principles, operational mechanisms, and applications of piston pumps in fluid power systems.
FR-L-074B-PC-25-NN-NN-N-3-S1N2-A1N-AAA-NNN-NNN
FRL074BPC25NNNNN3S1N2A1NAAANNNNNN
The fundamental design of piston pumps revolves around their basic components: the cylinder, piston, inlet and outlet valves, and drive mechanism. The cylinder houses the piston, which moves back and forth to create variations in volume, facilitating fluid intake and discharge. Piston pumps can be categorized into two main types: axial piston pumps and radial piston pumps.
83010304
Axial Piston Pumps: In axial piston pumps, pistons are arranged parallel to the pump shaft. When the shaft rotates, the pistons are pushed back and forth in a cylindrical chamber. This design leads to a more balanced distribution of forces, allowing for efficient operation at high pressures. Axial piston pumps are commonly used in high-performance hydraulic applications where precise control and high power density are essential.
Radial Piston Pumps: In radial piston pumps, the pistons are arranged radially around a central hub. As the hub rotates, each piston moves in and out of the cylinder, allowing for fluid transfer. Radial piston pumps are typically used in applications requiring lower flow rates but high pressure, such as automotive hydraulic systems and industrial machinery.
The operation of piston pumps relies on the principles of fluid dynamics and mechanics. As the piston moves downward in the cylinder, it creates a vacuum that opens the inlet valve, allowing fluid to fill the chamber. When the piston moves upward, it compresses the fluid, forcing it out through the outlet valve. This cyclical process ensures a continuous flow of hydraulic fluid, which is essential for powering hydraulic actuators, motors, and other components.
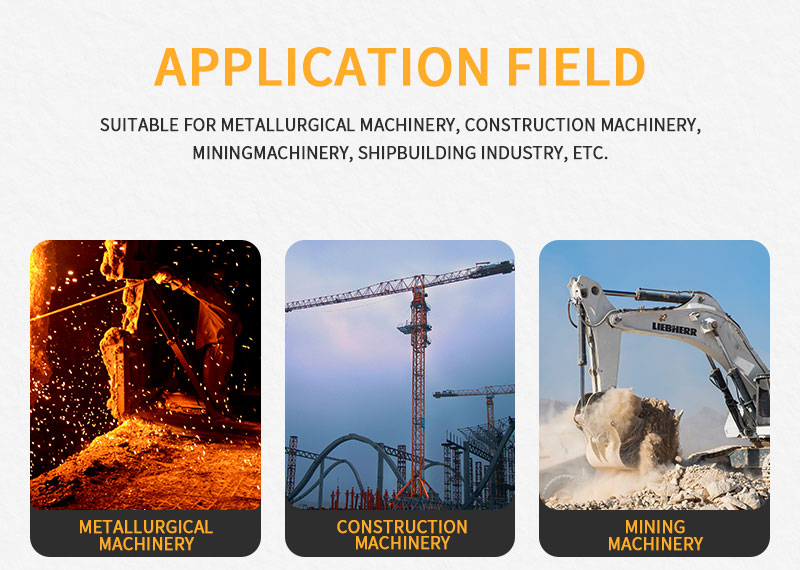
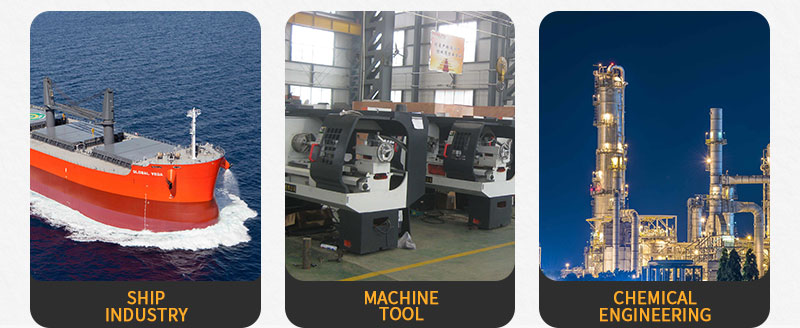