90R250KN5CD80S4C8K03NNN383824 piston pump
90R250KN5CD80S4C8K03NNN383824 piston pump

- Product Details
- Applicable Scene
Multi-stage hydraulic pumps are essential components in various industrial applications, where high pressure and efficiency are paramount. The design of such pumps involves a multitude of considerations to ensure performance, reliability, and durability. This article outlines the critical factors to consider when designing multi-stage hydraulic pumps.
90R250-KN-5-CD-80-S-4-C8-K-03-NNN-38-38-24
90R250KN5CD80S4C8K03NNN383824
One of the primary considerations in the design of multi-stage hydraulic pumps is the selection of materials. Materials must be chosen based on their mechanical properties and compatibility with the fluid being pumped. High-strength alloys or composites are often favored for their ability to withstand high pressures and resist corrosion. Additionally, the chosen materials should be easily manufacturable and cost-effective to ensure economic viability.
80005666
The hydraulic efficiency of the pump is heavily influenced by its geometry. Designing optimal impeller shapes and sizes is crucial for achieving high hydraulic performance. The number of stages in a pump directly affects the pressure output; however, an increase in stages may also lead to increased energy losses due to friction and turbulence. Therefore, balance must be struck between the number of stages and the overall efficiency of the pump.
Another critical aspect is the clearance between the rotating and stationary components. Tight clearances can enhance efficiency, but they may also lead to excessive wear and heat generation, particularly at high operating speeds. Conversely, wider clearances may reduce efficiency but increase the pump’s lifespan. Designers must determine the optimal clearance based on the anticipated operating conditions and service life requirements.
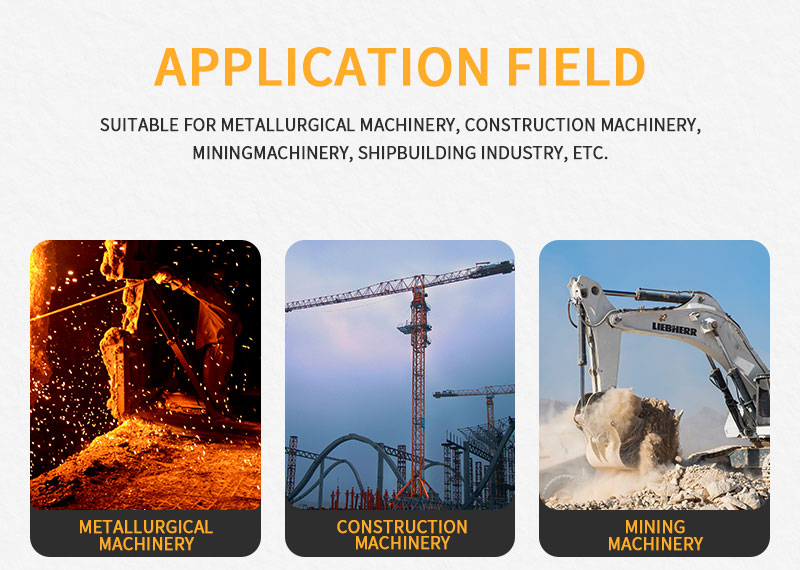
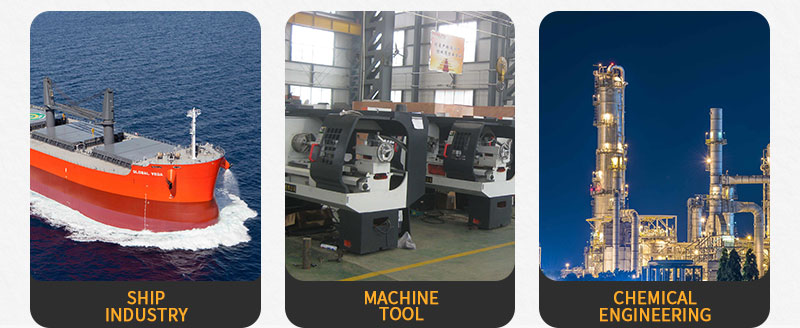