ERR130BLS2530NNN3S1NPA1NAAANNNNNN hydraulic pump
ERR130BLS2530NNN3S1NPA1NAAANNNNNN hydraulic pump

- Product Details
- Applicable Scene
To optimize performance and efficiency, engineers often use advanced computational fluid dynamics (CFD) simulations during the design phase. These simulations help in predicting flow patterns, identifying potential energy losses, and refining pump geometries to minimize turbulence. Additionally, maintaining an optimal fluid viscosity is crucial, as it influences the pump’s efficiency. Fluids that are too viscous can increase resistance to flow, while fluids that are too thin may cause inadequate lubrication and increased wear on pump components.
ER-R-130B-LS-25-30-NN-N-3-S1NP-A1N-AAA-NNN-NNN
ERR130BLS2530NNN3S1NPA1NAAANNNNNN
Another aspect to consider is the system design in which the hydraulic pump operates. Ensuring proper sizing of pumps, pipes, and reservoirs is critical to minimizing pressure drops and maximizing overall system efficiency. Moreover, implementing pressure control devices and variable-speed drives can enhance the adaptability of hydraulic systems, allowing them to respond efficiently to varying load demands.
83020343
Regular maintenance and monitoring are also vital for maintaining hydraulic pump performance. By routinely checking for leaks, monitoring fluid quality, and servicing mechanical components, operators can prevent performance degradation and costly downtime.
In summary, the performance and efficiency of hydraulic pumps are influenced by a combination of design, flow characteristics, system configuration, and maintenance practices. Understanding these factors allows engineers and operators to optimize hydraulic systems, improving productivity and reducing operational costs. As technology advances, the field of hydraulic pump design continues to evolve, promising even greater efficiencies and capabilities for the future.
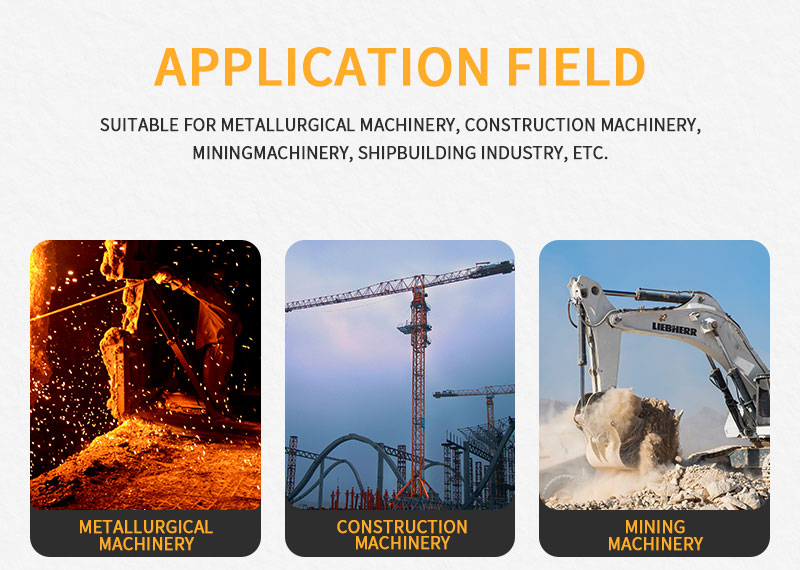
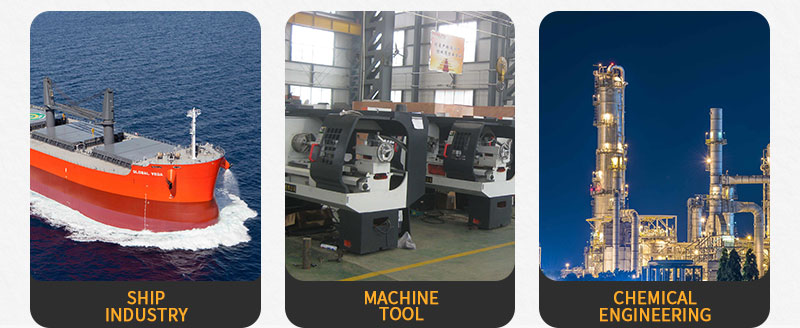