ERL147CLS2020NNN3K5NPA1NNNNNNNNNN hydraulic oil pump
ERL147CLS2020NNN3K5NPA1NNNNNNNNNN hydraulic oil pump

- Product Details
- Applicable Scene
Plunger pumps are essential components in various industrial applications, ranging from hydraulic systems to chemical processing. Their durability is critical not only for operational efficiency but also for reducing maintenance costs and downtime. One of the most significant factors affecting the durability of plunger pumps is the selection of materials used in their construction. This article explores how material selection influences the reliability and lifespan of plunger pumps.
ER-L-147C-LS-20-20-NN-N-3-K5NP-A1N-NNN-NNN-NNN
ERL147CLS2020NNN3K5NPA1NNNNNNNNNN
The operating conditions of plunger pumps can be extremely demanding. They often work under high pressures and can pump a variety of fluids, which may include abrasive, corrosive, or viscous materials. Therefore, selecting the appropriate materials for the pump’s components, such as the plungers, cylinders, seals, and other parts, is crucial.
7000671
Firstly, the selection of materials affects wear resistance. Plungers and other moving parts are subject to friction and wear during operation. Harder materials, such as high-carbon steels or ceramic composites, can provide better wear resistance, thus extending the life of the pump. On the other hand, softer materials may lead to increased wear, resulting in frequent replacements and repairs.
Corrosion resistance is another vital consideration, especially when pumps are used to handle corrosive fluids. Materials such as stainless steel, specialized alloys, and plastic composites may be chosen to withstand chemical attack. If inappropriate materials are used, corrosion can lead to structural failure, leaks, and ultimately, pump failure. For instance, using standard carbon steel in a pump designed to handle acidic fluids can result in rapid degradation and expensive downtime.
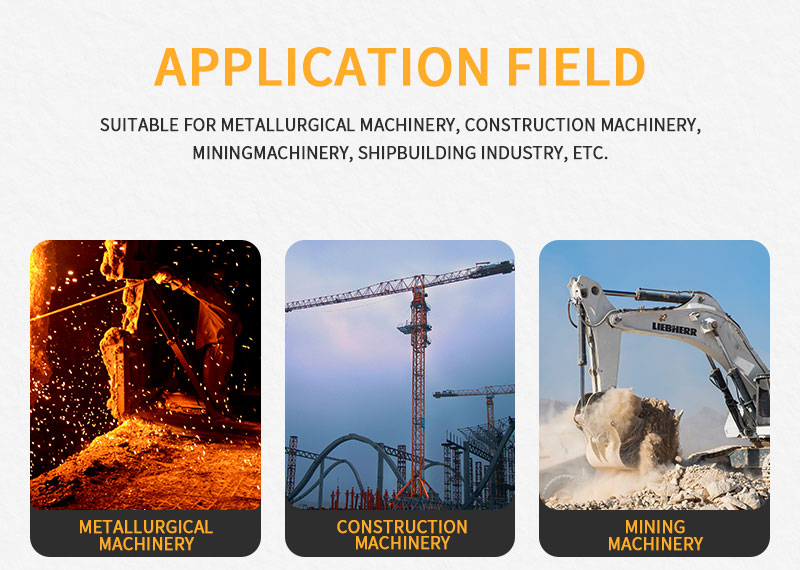
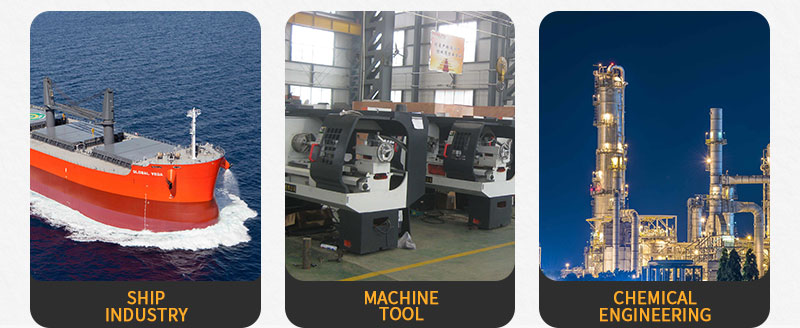