ERL147CLS2020NNN3S4NLA1NNNNNNNNNN hydraulic oil pump
ERL147CLS2020NNN3S4NLA1NNNNNNNNNN hydraulic oil pump

- Product Details
- Applicable Scene
Hydraulic pump cavitation is a common issue faced in low-pressure fluid systems that can lead to inefficient operation, equipment damage, and increased maintenance costs. Understanding how to identify and mitigate this problem is essential for maintaining optimal system performance. In this article, we will explore the causes of cavitation, its effects, and effective strategies to resolve the issue.
ER-L-147C-LS-20-20-NN-N-3-S4NL-A1N-NNN-NNN-NNN
ERL147CLS2020NNN3S4NLA1NNNNNNNNNN
Cavitation occurs when the pressure in a fluid system drops below the vapor pressure of the fluid, causing the formation of vapor bubbles. These bubbles can collapse violently when they move into higher-pressure regions of the system, leading to shock waves that can cause significant damage to hydraulic components. In low-pressure systems, the relative inefficiencies and fluctuations can exacerbate the risk of cavitation.
7000547
The primary causes of hydraulic pump cavitation include insufficient inlet pressure, high fluid temperature, and the presence of contaminants. To combat cavitation effectively, it is crucial to examine these factors closely.
One of the first steps in solving cavitation is to ensure that the hydraulic pump has sufficient inlet pressure. This can be achieved by:
Reducing the distance between the hydraulic reservoir and the pump: Shortening the distance reduces the pressure loss due to friction, helping maintain adequate suction.
Increasing reservoir fluid levels: A higher fluid level in the reservoir ensures that the pump has access to enough fluid, reducing the likelihood of air entering the system.
Utilizing larger diameter piping: Larger pipes can minimize pressure drop caused by fluid flow, thereby increasing the inlet pressure required for pump operation.
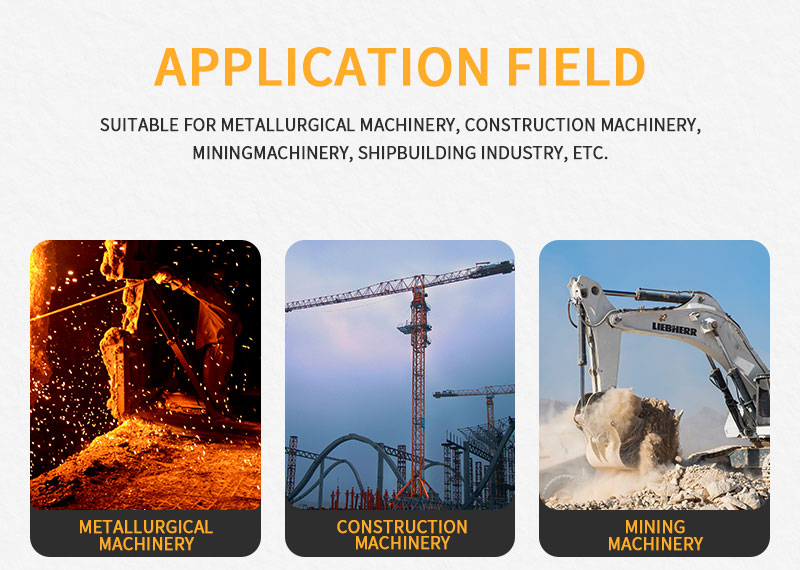
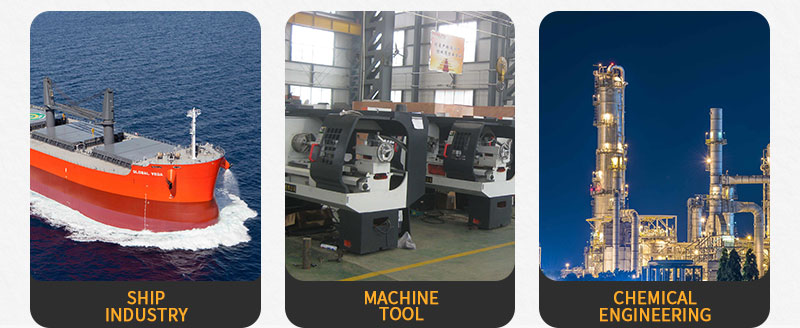