ERL147CLS2420NNN3S1RPA1NNNNNNNNNN hydraulic pump
ERL147CLS2420NNN3S1RPA1NNNNNNNNNN hydraulic pump

- Product Details
- Applicable Scene
Cavitation is a common issue in hydraulic pump systems, leading to reduced efficiency, increased wear, and potential failure of equipment. Understanding the causes of cavitation and adopting preventive measures is essential for maintaining the integrity of fluid systems. This article outlines key strategies for identifying and resolving hydraulic pump cavitation problems.
ER-L-147C-LS-24-20-NN-N-3-S1RP-A1N-NNN-NNN-NNN
ERL147CLS2420NNN3S1RPA1NNNNNNNNNN
Cavitation occurs when the local pressure in a fluid drops below its vapor pressure, leading to the formation of vapor bubbles. These bubbles collapse violently when they move into higher-pressure regions, resulting in shock waves that can erode metal surfaces and degrade pump performance. To solve cavitation issues, it is crucial to identify their root causes:
83061754
Check System Pressure: Ensure that the inlet pressure to the pump is sufficient. Low inlet pressure can lead to cavitation. Implement systems to monitor pressure effectively and ensure that the pump is always supplied with adequate fluid.
Reduce Pump Speed: High rotational speeds can create significant pressure drops at the pump’s suction side. If possible, reduce the pump speed to maintain sufficient pressure. This change can also lower the volume of fluid, optimizing flow while minimizing cavitation risks.
Increase Fluid Temperature: The vapor pressure of fluids increases with temperature. By raising the temperature of the hydraulic fluid, you can decrease the likelihood of cavitation. However, this must be balanced with the properties of the fluid and the system’s thermal management capabilities.
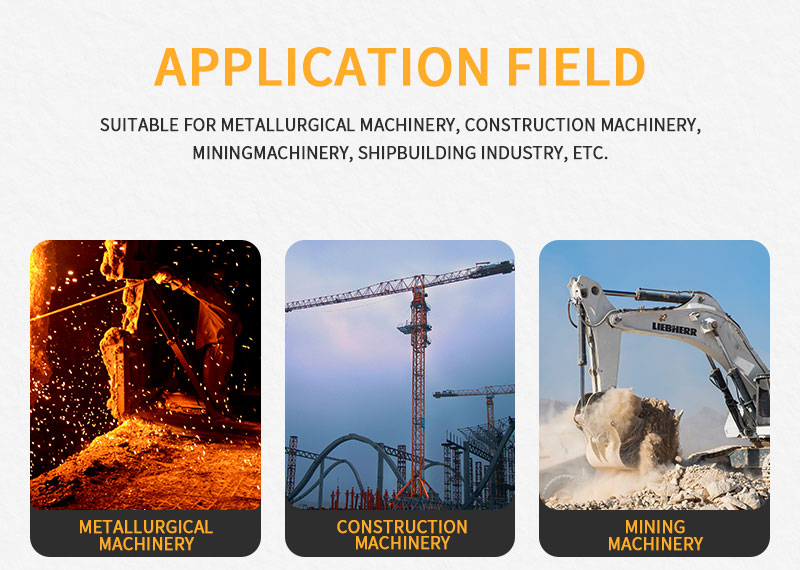
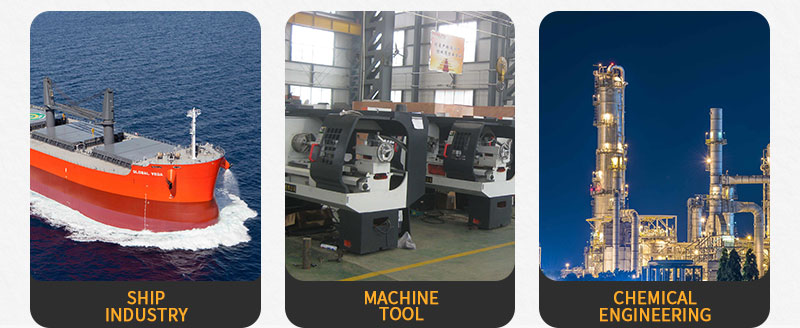